Quality Control & Anilox Maintenance
Quality Statement
Apex International is dedicated to manufacturing all our products in accordance with our customers’ expectations and OEM specifications.
Claim Handling
If you receive a product that does not meet the required standard, follow the procedure outlined on our QCR to ensure a fast resolution is achieved.
Service / Maintenance
To ensure longevity and high print quality, it is essential to handle your anilox with care throughout their lifecycle.
Cleaning
Regular and proper cleaning of your anilox roll/sleeve is essential to maintain high print quality and prolong their lifespan.
Warranty Disclaimer for Under-Corrosion and Construction
At Apex International, we are dedicated to manufacturing all our products in accordance with our customers’ expectations and OEM specifications. We take pride in ensuring the highest quality standards are consistently met throughout every stage of the production process. Our commitment to Quality Control & Assurance (QCA) is evident in our daily calibration of measurement tools, such as microscopes and micrometers, and our cutting edge innovative internal calibration process. Additionally, we regularly send test samples of our coatings to leading universities for independent assessment and validation. Our production staff undergoes comprehensive training on the QCA standards necessary for full product traceability. However, in the unlikely event that you receive a product from Apex that does not meet the required standard, please follow the procedure outlined on the backside of our Quality Control Report (QCR) to ensure a fast resolution is achieved.
Warranty
This Limited Warranty applies to physical goods, including anilox rolls, anilox sleeves, glue sets, and other goods purchased from Apex International. Upon receipt of a claim, accompanied by all the associated information and images, Apex will conduct an urgent internal investigation. Following the initial internal assessment, if required, Apex will arrange transportation for the product and conduct a thorough physical investigation and assessment.
Coverage
This Limited Warranty covers our products against under-corrosion and body construction, provided that products are used under standard industry working conditions with recommended maintenance, cleaning, and storage practices followed throughout the Warranty Period.
Apex International will repair or replace, at no charge, products or parts that are proven defective due to material failure or poor workmanship.
Exclusions
This Limited Warranty does not cover:
- Problems caused by poor storage conditions.
- Problems caused by misuse of the product.
- Problems caused by aggressive cleaning methods.
- Products and specifications that have been purchased against the technical advice of Apex.
Correction of Problems
Apex International will either repair the product using new or refurbished replacement parts or replace it with a new product, at our discretion.
Warranty Period
The under-corrosion warranty period for our products is one year (365 days) from the date of invoice. Any replacement physical good or parts will only assume the remaining warranty period of the original order.
Claim Handling
Step 1
Claim Procedure In the unlikely event that our product does not meet your expectations, please follow these steps:
Provide detailed information about the problem, including photos, videos, and a print sample if applicable. Ensure to include the Apex reference numbers (AB/W/C numbers) for immediate investigation. Send this information to the relevant internal department listed below:
Step 2
If the product needs to be returned to Apex, ensure it is cleaned and securely packed with the Return Merchandise Authorization (RMA) number clearly labeled on the crate. Apex will provide collection information.
- Apex Europe, Hapert/NL
quality@eu.apexinternational.com | Tel. + 31 497 361111 - Apex Italy, Olgiate Olona/Italy
quality@it.apexinternational.com | Tel. + 39 0331 379 063 - Apex Latin America, Paraná/Brazil
quality@la.apexinternational.com | Tel. 55 41 3677 2678 - Apex Asia Pacific, Nashik/India
quality@ap.apexinternational.com | Tel. 91 2 551 66 111 - Apex North America, Donora/USA
quality@na.apexinternational.com | Tel. 1 724 379 8880 - Apex Keller Dorian, Jonage/France
quality@kdg.apexinternational.com | Tel. 33 472 681500 - Apex Panhuizen, Hapert/NL
quality@pnh.apexinternational.com | Tel. 31 492 538534
Step 3
Upon receipt of the above information and product, Apex will conduct a full inspection based on your input and advise on the solution. If applicable, replacement products will be provided within a three-week period.
Service & Maintenance
Use & Care of Anilox Rolls/Sleeves
The anilox is considered the heart of the flexographic printing press, transferring a precise amount of ink from the reservoir to the printing plate. To ensure longevity and high print quality, it is essential to handle your anilox with care throughout their lifecycle.
Handling upon Arrival
- Inspect the crate for any damage upon arrival. If damage is observed, notify the carrier immediately and take photos as proof.
- Remove the anilox from the crate and protective wrap, inspecting for any damages.
- If transport damage is identified do not discard packing material and notify Apex accordingly.
Installing into the Press
- Handle the anilox with care, supporting it from the journals, if applicable.
- Cover the body with a protective wrap when installing into the press to prevent damage to the engraved surface.
In the Daily Production Process
- Avoid running the anilox dry with the ink chamber loaded against it to prevent excessive wear and scoring.
- Keep the anilox running when ink is in the chambers to prevent cell blockages.
- Follow proper cleaning instructions using appropriate chemical cleaners with a pH value between 5 and 10.
- Store aniloxes covered in a rack or original crate, ensuring the surface is clean and dry.
For additional advice on anilox and mechanical deep cleaning procedures, please contact your local Apex agent.
Cleaning
Cleaning of Anilox Rolls/Sleeves Regular cleaning of your anilox is essential to maintain high print quality and prolong their lifespan. Cleaning should be performed immediately after a press run to prevent ink buildup within the cells, which can affect print consistency.
For daily cleaning:
- Use clean water, alcohol-based solvent, or chemical cleaners with a pH value between 5 and 10.
- Apply the chosen cleaning agent onto the roll surface and allow it to soak.
- Use a steel brush for ceramic anilox to brush the surface in a circular motion with maximum pressure.
- Rinse the roll with clean hot water or solvent, wipe it down, and ensure it is dry before storage.
Note: Avoid using chlorine, ammonia, or highly acidic cleaning liquids, as they can damage the ceramic layer and cause corrosion. For further guidance on cleaning procedures or product support, please consult your local Apex production facility.
DOWNLOAD OUR FREE ANILOX USE & CARE GUIDE
The anilox is considered the heart of the flexographic printing press, transferring a precise amount of ink from the reservoir to the printing plate. To ensure longevity and high print quality, it is essential to handle your anilox with care throughout their lifecycle. How? Follow the instructions in the free Anilox Use & Care Guide!
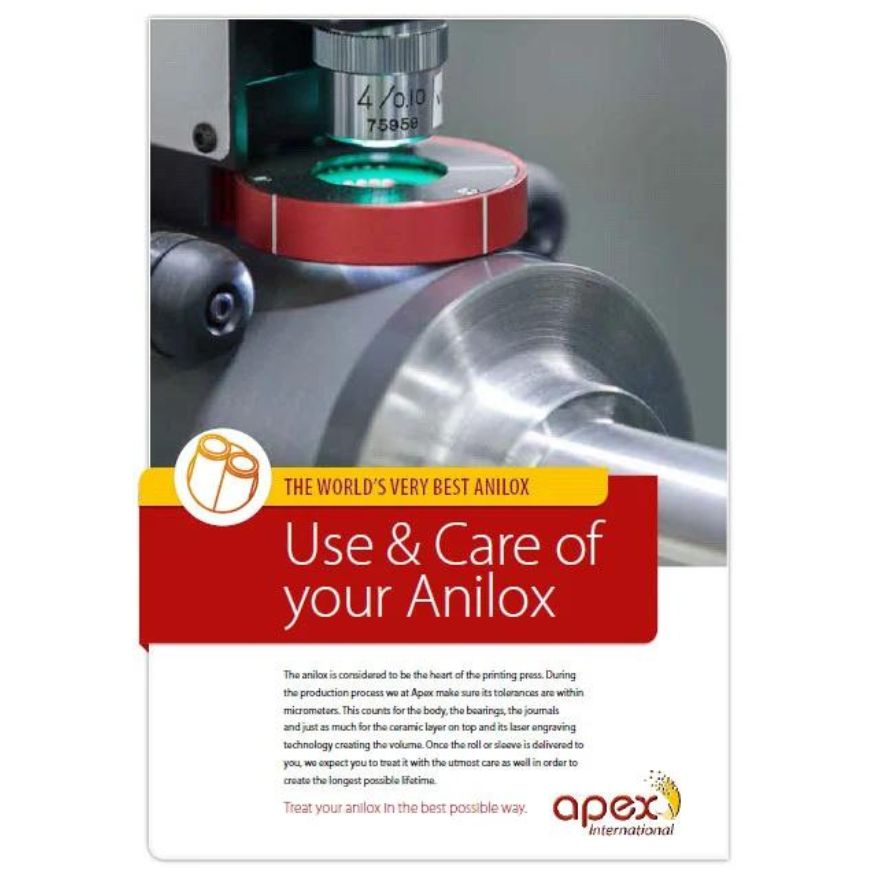